Story and photos by Paul Duncan (this article originally appeared in the January-February 2021 edition of the Enchantment Flyer).
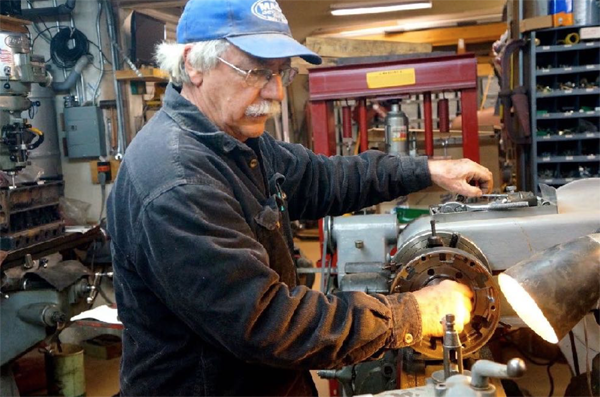
Larry Azevedo working on a lathe in his Shop. He is making small adjustments on
the brake drum bushing during rebuild of the Duncan 1926/1927 engine.
Following the COVID-19 “Lock down” and restrictions on group gatherings, Larry re-opened his shop for small groups in July. During our “stay at home home”, Marilyn and I discovered that we finally had time to work on one of our previously-delayed Model T projects. We found that the engine in our 1918 Model T Touring Cut-Off had no compression. Fortunately, we had a late-model engine purchased several years ago from Brian Dean that could be a more practical engine to restore. Ten years ago, we had restored our 1920 Touring T engine when Larry first began restoring engines for Club members in his Corrales Shop.
Since then, he has rebuilt 35 engines. The process in 2020 was similar with regards to using oversize pistons and valves. I soon realized that there was a major difference how we did the flywheel, magneto and transmission rebuilding balancing and alignment. Although the 1920 engine, transmission and magneto were in better condition, Larry explained that over the intervening 10 years he has improved and refined his techniques regarding alignment of the transmission. He told me that he had discussed these alignment techniques with Mike Bender in Tulsa. He referred me to Mike’s website: www.ModelT-Tips.com that is on YouTube. These Model T Tips are well done and include lots of important information about the restoration process of a Model T engine and associated components.
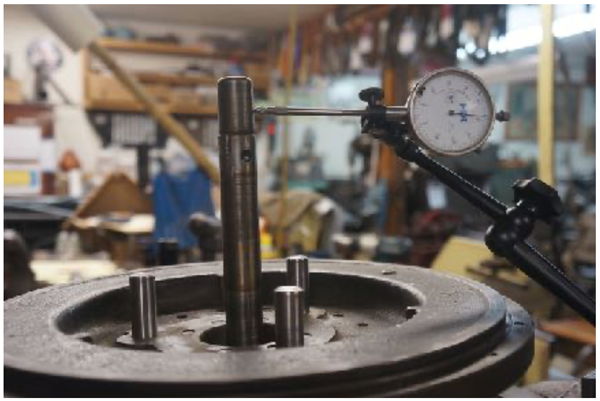
I asked Larry to explain some of the secrets of the Model T’s mechanical success that he had learned over his 50 years working on them. He said: The use of precision measurement techniques was a major reason for Henry Ford’s success. He went on to explain the role that a Swedish engineer, Carl Edvard Johansson (1864-1943), had on Henry’s thinking. Johansson invented the gauge block set, also known as “Jo Blocks.” In 1923 Ford purchased Johansson’s company. Ford had used the technology that Johansson had first pioneered in Sweden in 1896 and patented in 1901.
In a publication entitled The Ford Industries-Standards of Standards it states: Production methods used in the manufacture of Ford automotive units require that every part must be machined within close predetermined limits or variations in size, so that when they are delivered to the assembly line in domes’c or foreign plants or use by Ford dealers for replacements, component parts will go together with the proper fit to obtain the best results from the assembled product. The accuracy specified on all parts of Ford automotive units is accomplished and maintained through the use of commercial and specially designed apparatus knows as machine tools. Jigs, fixtures, production and gauging tools that have been certified as to size with master standard gauges are accurate within less than 4 millionths of an inch (0.000004″). The production of parts as outlined above is known as interchangeable manufacturing, which means that all parts required to make two or more complete units can be assembled without preliminary fitting or checking.
In movies of the Model T assembly produced by Ford Motor Company (Link to book review (pg. 7) in the Jan.-Feb. 2021 Enchantment Flyer) one observes the workman reaching into boxes of parts on the assembly line and assembling the transmission. They don’t take the time to check the fit because they know it will fit and run as designed. The precision gauge blocks mentioned above are called Johansson gauge blocks. At the time, they were the ‘World’s Standard of Measurement of length and have no counterpart in science or in industry.
The more I am around Model T’s, I continue to learn that the Model T, although mass produced, was a finely-tuned machine made with precision. With proper attention to detail in the shop today, one can obtain that same or better precision. Larry emphasized the steps he is now taking to be absolutely sure in the concentricity of the transmission shaft, for instance. When we recently bolted the transmission shaft flange to the flywheel, we had less than the diameter of a human hair (3 thousands of an inch) runout or essentially an absolutely straight and perpendicular shaft in relation to the crankshaft flange. This was his goal. I understood a lot more about the measurements having reviewed Mike Bender’s YouTube presentations. We also replaced both the Reverse and Brake drums with new ones from Dave Nolting’s shop in Ohio because the original drums were both cracked.
Many readers know that Larry Azevedo worked at Sandia Laboratories for 30+ years. He earned a Ph.D. in solid-state physics from UCLA and during his first years at Sandia worked in low temperature research. For his last twenty years he put his objective and mathematic skills to use as manager of measurement standards at Sandia. This lab certified the accuracy of all measurements undertaken across the U.S. Department of Energy.